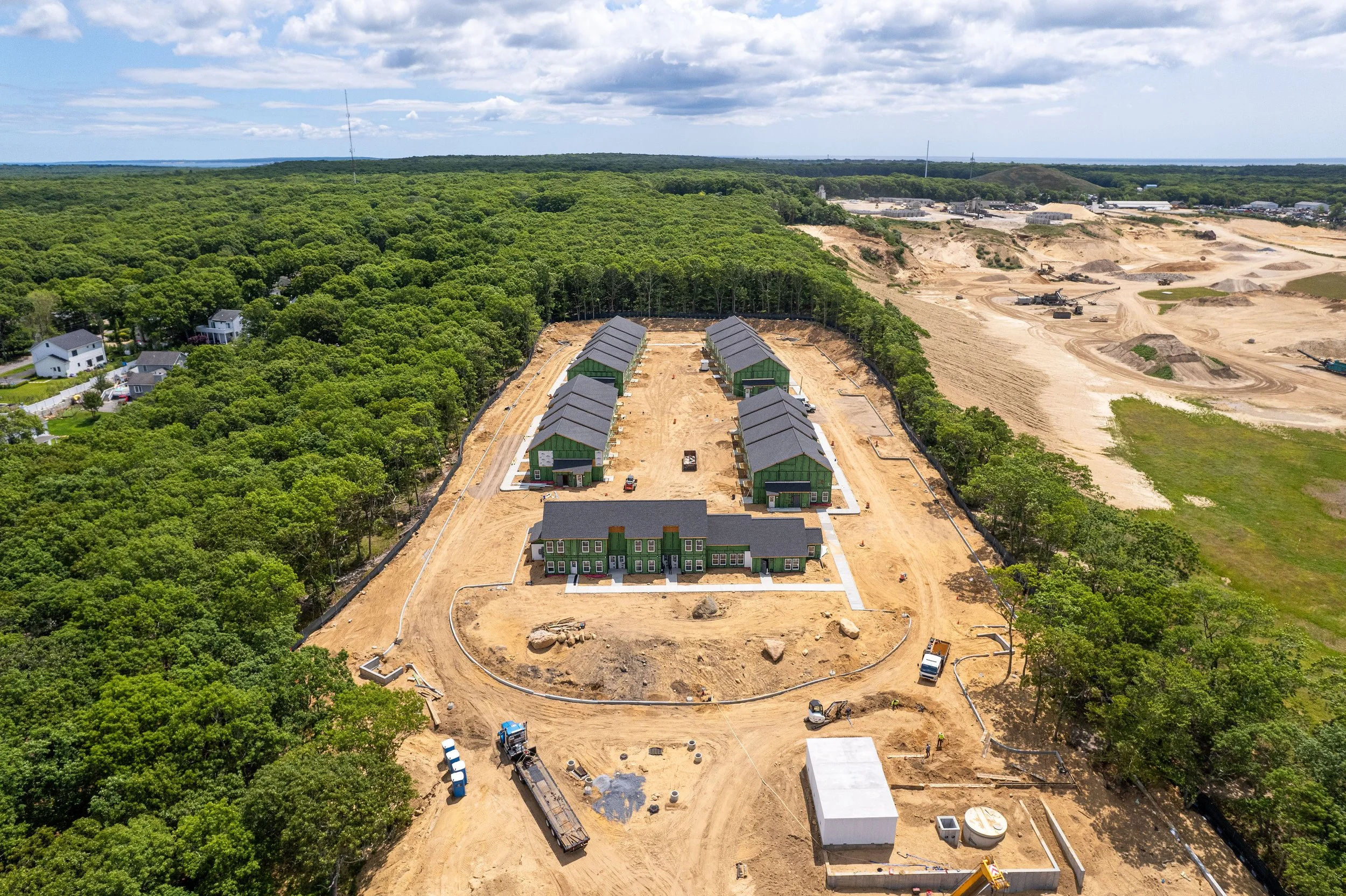
GGV SPOTLIGHT
Modular Building Q&A
As an early adopter of modular housing on Long Island, Georgica Green Ventures understands its many benefits—safety, sustainability, and reliability. Our Vice President of Design, Crystal Chan, shares her insights on how modular building helps us achieve our goals.
Q: What is modular housing? What are the benefits?
A: Modular construction is a method where sections or modules of a building are constructed off-site, then transported to the final location for assembly. Using modular construction for our housing developments gives us a high level of control in terms of quality, schedule, safety, and cost. With construction completed in a repetitive and efficient production line within the weather-protected environment of a factory, we reduce material waste and mitigate weather-related delays. Most importantly, we minimize construction-related impact to our neighbors while providing a safe and controlled environment for our builders.
Q: Give us an example of all this applied in a development?
A: Sure, let’s look at The Green at Gardiner’s Point, as an example that we’re developing with our partner East Hampton Housing Authority on eight acres. Located in East Hampton in a residential community near Three Mile Harbor—the development is surrounded by nature, but it's only being served by a 2-lane road. Between the traffic generated on local roads, the legendary Long Island “trade parade” and the lack of parking, our construction project would have added a noticeable burden to the already unmanageable traffic.
Obviously, this speaks to the need for workforce housing on the East End, which when complete, this development itself will help to address! By utilizing modular construction on this project, we are creating less community disturbance, lessening traffic burden, noise pollution and our project's impact on local wildlife, the environment, and our neighbors. Having more control of our schedule without weather-related delays allows us to optimize our construction planning in terms of cost, timing and safety.
“The flexibility within the design allows for aesthetic choices as well as variations in unit types—studio, one-bedroom, two-bedrooms. All are achievable in the modular framework.”
Q: How involved is GGV in determining the design of the modular housing? Do you have the flexibility to make design decisions, or are you limited to predefined formats?
A: Modular building is not limited to a specific template, we are essentially limited only by our transportation, i.e. the dimensions of a flatbed truck. Within this parameter, the modular geometry allows for a variety of unit types —studio, one-bedroom, two-bedrooms. This is in addition to the limitless aesthetic choices on the interior and exterior of the buildings. Essentially, we are using a “factory solution” for our custom problem, where the bones of the units are modular, but the exterior design will vary widely in effort to produce context-specific design that is suitable within the local architectural aesthetic. For example, mid-rise projects in more urban locations may look more streamlined and modern while projects in traditionally single-family communities may evoke a cottage or farmhouse aesthetic.
Q: What is done with the cost savings?
A: The cost savings generated from modular construction allows us to invest in additional features that benefit our resident’s experience and the environment beyond the minimum that is required by codes and regulations. For example, we often use higher quality fixtures and materials that are more durable and generate less construction waste because fewer replacements are needed) and are more efficient (less utility cost burden to our residents). Where feasible, our projects are equipped with solar panels or are “solar-ready”. This comprehensive approach to cost and value optimization allows us to demonstrate that it's possible to create a high quality affordable housing project without a luxurious budget.
Q: Why is factory produced modular construction safer?
A: Modular construction is safer for workers because it takes place within controlled environments, reducing exposure to weather-related hazards, and can utilize standardized processes akin to assembly lines, minimizing risks associated with traditional on-site construction activities.
Q: How does modular construction affect the local workforce?
A: Since the modular components are assembled together into the whole building on site, and we construct the project-specific facade and exterior elements on site, construction tradespeople are still needed as part of our building process. From initial site work preparation through final completion, local talent including electricians, plumbers, mechanical contractors, painters, roofers, window and flooring installers, fire and life safety subcontractors and many other trades are needed to finish the project.
The Green at Gardiner’s Point caption here.